a house among the gumtrees. with water views (preferably not just temporary ones)! – ocean views even, perhaps? on a hill – the view is better from up high. who wouldn’t love that.

we are certainly in favour of that idea, and while we don’t necessarily have to fear floods the other constant aussie threat will definitely affect our planning: bush fire. these days there are many ways to build a fire resistant home, but most of them utilise materials some would not consider environmentally friendly, and therefore we have decided to go with a somewhat unconventional approach.

our home will (mostly) have hemp outer walls. it doesn’t look very fire resistant, right? in this shape, as hurd, it isn’t: this is the raw material, the mashed up stalks of the hemp plant … but mix those up with lime, sand and binder (apparently it’s a secret formula), let it cure and you can hold a blow torch to it – it won’t burn.

this hemp mixture has a few other desirable properties as well: it is an acceptable heat bank (especially given the wall thickness is 300 mm), but also a decent insulator, and it is not a moisture barrier, with is a great advantage in modern well insulated homes, where condensation and mould often become issues.

and it also has this great organic look. the walls will of course be rendered, but the render can be transparent, leaving the patters visible, at least if the tamping has been done well. tamping is very important: tamp too loosely and bits of wall may fall out, tamp too hard and it’s wasting material and potentially compromising the insulating capacity of the wall. it’s also not a good idea to try and add more than 10-15 cm at a time, otherwise it becomes difficult to ensure the material is tamped to the same consistency all the way through.

building hemp walls is hard work: all the material, in our case about 65 cubic meters of it, needs to be mixed, carried, lifted, loaded into the formwork, tamped (firm but spongy) and left to cure for a few weeks. one load in the 300 liter barrel of the mixer contains about 15kg of hurd, 8 kg lime, 27 kg of binder, 10 kg sand and about 40 kg water – approximately 100 kg all together. the formwork can come off after a day or two; the outer boards stay, the inner ones are moved up.

the hemp then hardens, but very slowly. concrete takes a few weeks to cure, hemp takes many years. in the meantime it continues to absorb carbon dioxide, tons of it. the material is environmentally friendly in more than one way.

this is our neighbours house, and we just spent a little time helping out. it’s a great learning experience for us: kris & nat learned how to tamp the walls to make them look as good as those in the photo above, and i got to prepare the hemp mix. btw the lime is vicious stuff.
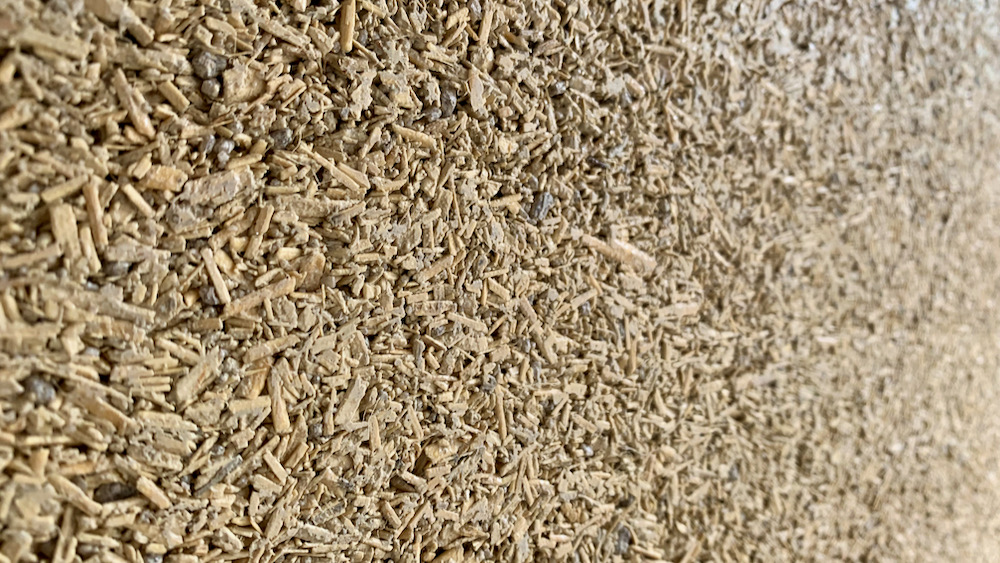
a few more weeks and we get to practise on our own home.